Golf balls are made through a multi-step process involving core creation, layering, and dimple patterning. Manufacturers use various materials to optimize performance.
Golf ball production begins with the core, often made from rubber or synthetic materials. This core determines the ball’s compression and distance capabilities. Next, layers of different materials are added around the core to enhance spin, control, and durability. The outermost layer, known as the cover, is typically made from urethane or surlyn.
Finally, the ball’s surface is patterned with dimples, which improve aerodynamics and flight stability. Each step in the manufacturing process is carefully controlled to ensure consistency and quality. Advances in technology and materials continue to evolve, leading to better-performing golf balls for players of all skill levels.
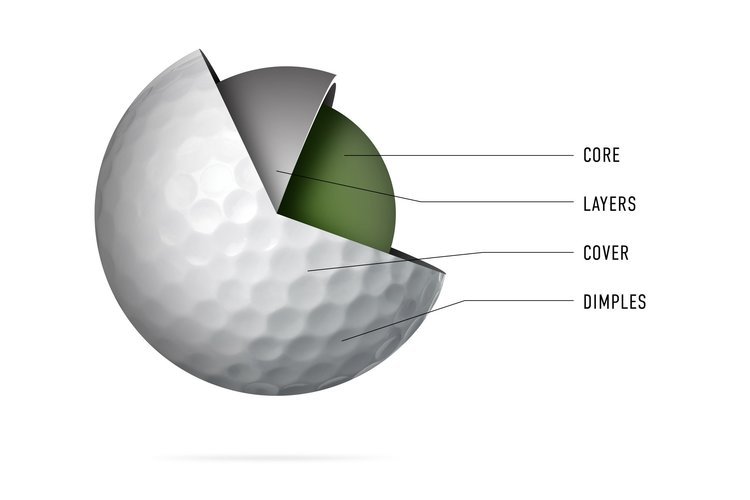
Credit: golfstatus.com
Introduction To Golf Ball Manufacturing
Golf is a beloved sport enjoyed by many. The golf ball is a key element. Understanding its creation enhances appreciation. This guide dives into the process. We will explore its history and importance.
Brief History
The golf ball has evolved significantly. In the 14th century, wooden balls were used. By the 17th century, feather-filled leather balls appeared. These were known as “featheries”. In the 19th century, gutta-percha balls gained popularity. They were more durable and cost-effective. Today, modern golf balls use advanced materials and technology.
Importance In The Sport
The golf ball’s design impacts gameplay. It affects distance, accuracy, and control. Different balls suit different playing styles. Professional players often choose specific brands. Beginners may prefer versatile options. The ball’s construction includes layers, core, and cover. Each part influences performance.
Core Materials
The core of a golf ball plays a crucial role in its performance. It affects the ball’s speed, distance, and feel. Understanding the core materials helps in choosing the right ball for your game.
Rubber Composition
The most common material for golf ball cores is rubber. Rubber is durable and provides excellent energy transfer. Manufacturers use different types of rubber to tweak performance.
- Natural Rubber: Offers a soft feel and good control.
- Synthetic Rubber: Provides better durability and higher speeds.
Natural rubber has been used for decades. It gives a softer feel, which is preferred by many golfers. Synthetic rubber is more recent and aims to improve durability and performance.
Synthetic Alternatives
Besides rubber, there are synthetic alternatives for golf ball cores. These materials aim to enhance specific features like distance or control.
- Polybutadiene: Known for high energy transfer and distance.
- Polyurethane: Offers a soft feel and good spin control.
Polybutadiene is a popular choice for distance-focused golf balls. It offers high energy transfer, leading to greater distance. Polyurethane is preferred for its soft feel and excellent spin control. It is often used in premium golf balls.
Each material has its unique benefits. Understanding these can help you choose the right ball for your game.
Core Formation
The core of a golf ball is its powerhouse. It determines the ball’s distance and control. The core formation process involves molding, applying pressure, and heat. Let’s dive into each step.
Molding Process
The molding process starts with raw rubber materials. These materials are mixed with chemicals. The mixture is then placed into molds. The molds shape the core into perfect spheres. The size and weight must be consistent. This consistency ensures the ball performs well.
Pressure And Heat Application
After molding, the cores undergo pressure and heat application. This step is crucial. It solidifies the core and enhances its properties. The cores are placed in a press machine. The machine applies high pressure and heat. This process takes a few minutes.
The pressure makes the core denser. The heat helps the rubber to bond well. This combination gives the core its strength and elasticity. These properties are vital for a golf ball’s performance.
Table of Pressure and Heat Values:
Step | Pressure (PSI) | Temperature (°C) |
---|---|---|
Initial Molding | 1000 | 150 |
Final Pressing | 2000 | 170 |
Once the cores are set, they cool down. The cooling process stabilizes their shape. The cores are now ready for the next stage of ball making.
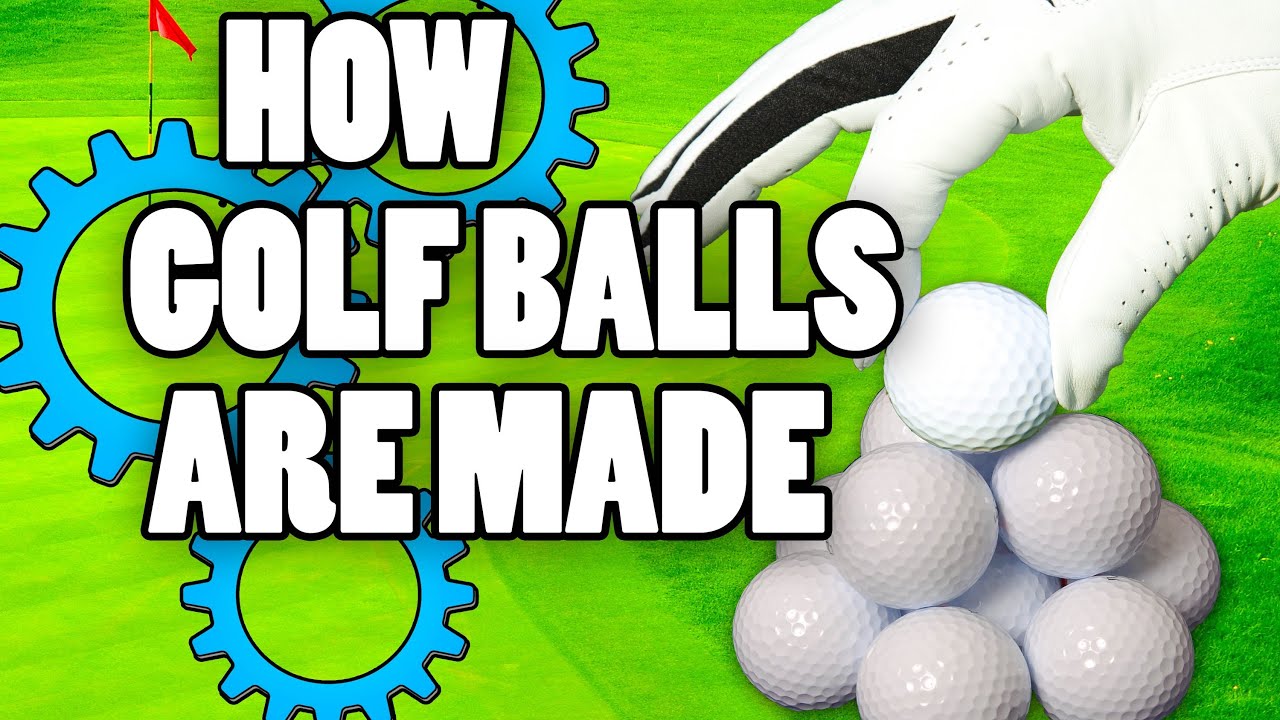
Credit: www.youtube.com
Mantle Layer
The mantle layer is crucial in a golf ball’s construction. It sits between the core and the cover. This layer impacts performance, distance, and control.
Purpose And Function
The purpose of the mantle layer is to optimize performance. It enhances the ball’s distance and control. This layer ensures energy transfer from the core to the cover.
The mantle layer also helps in maintaining the ball’s shape. It reduces spin for longer shots. This is essential for achieving desired flight paths.
Materials Used
Various materials are used in the mantle layer. Manufacturers choose materials based on desired performance. Common materials include:
- Thermoplastic elastomers
- Ionomers
- Polybutadiene
Thermoplastic elastomers add durability. Ionomers provide a balance of distance and control. Polybutadiene enhances energy transfer.
Each material has unique properties. These properties affect the ball’s performance. The choice of material is vital for achieving optimal results.
Cover Layer
The cover layer of a golf ball is essential. It impacts the ball’s durability, spin, and feel. Different materials and techniques are used to create the cover layer. Let’s dive into the details.
Types Of Covers
Golf ball covers come in two main types:
- Surlyn: A durable and affordable plastic. It offers less spin.
- Urethane: A softer material. It provides more spin and control.
Manufacturing Techniques
There are various methods to manufacture golf ball covers. Here are the most common:
- Injection Molding: Plastic is melted and injected into molds. This method is fast and precise.
- Compression Molding: Pre-formed plastic sheets are heated and pressed. This creates a tight and durable cover.
Method | Advantages | Disadvantages |
---|---|---|
Injection Molding | Fast, precise | Expensive setup |
Compression Molding | Durable, tight fit | Slower process |
Understanding these manufacturing techniques helps in choosing the right golf ball. The cover layer plays a crucial role in performance. Choose wisely to match your playing style.
Dimple Design
The dimple design on a golf ball is crucial. It affects the ball’s flight, distance, and overall performance. Each golf ball has a unique pattern of dimples. These patterns are meticulously crafted and tested.
Aerodynamics
Dimples on golf balls improve aerodynamics. They reduce air resistance during flight. This helps the ball travel farther. Smooth balls would not travel as far. Dimples create a thin layer of air around the ball. This reduces drag and increases lift.
Impact On Performance
The dimple design impacts performance in several ways. It affects the ball’s speed, spin, and trajectory. Different dimple patterns suit different playing styles. Golfers choose balls based on these characteristics.
- Speed: More dimples can increase speed.
- Spin: Specific patterns can control spin.
- Trajectory: Dimples help maintain a steady flight path.
Manufacturers use various dimple designs to achieve these effects. This makes each golf ball unique. The right dimple design can improve a golfer’s game significantly.
Quality Control
The quality control of a golf ball ensures it meets high standards. This process guarantees consistency, durability, and performance. Let’s dive into the different aspects of quality control.
Testing Procedures
Quality control involves various testing procedures. Each golf ball undergoes rigorous tests to check its integrity. These tests include:
- Compression Test: Measures the ball’s flexibility.
- Durability Test: Ensures the ball withstands repeated use.
- Distance Test: Assesses how far the ball travels.
- Spin Test: Evaluates the ball’s spin rate.
Regulatory Standards
Golf balls must meet regulatory standards set by governing bodies. These standards ensure fair play. Important organizations include:
- The USGA: United States Golf Association.
- The RA: The Royal and Ancient Golf Club.
Both organizations have strict guidelines. These cover:
- Ball weight and size.
- Ball velocity and distance.
- Ball symmetry and construction.
Golf ball makers ensure compliance through detailed testing. This keeps the game fair and enjoyable for all players.
Environmental Considerations
Understanding how a golf ball is made involves more than just its design and materials. Environmental considerations play a crucial role in modern manufacturing processes. Companies are adopting sustainable practices and focusing on recycling efforts to reduce their ecological footprint.
Sustainable Practices
Golf ball manufacturers are now prioritizing sustainable practices to minimize environmental impact. Many are switching to eco-friendly materials that are biodegradable. These materials help in reducing landfill waste.
Some companies use renewable energy sources in their production plants. Solar and wind energy are popular choices. This shift helps in lowering carbon emissions significantly.
Here’s a quick look at the sustainable practices adopted:
- Use of biodegradable materials
- Adoption of renewable energy
- Implementation of water-saving technologies
Recycling Efforts
Recycling efforts are another critical aspect. Manufacturers are increasingly recycling old golf balls. Recycled materials are used to create new balls, reducing the need for raw materials.
Companies also encourage golfers to return used balls. This helps in creating a circular economy. Some brands even offer discounts for returned balls.
Here is a table showcasing the benefits of recycling efforts:
Benefit | Description |
---|---|
Reduced Waste | Less waste in landfills |
Resource Conservation | Lower need for new raw materials |
Cost Savings | Discounts for returned balls |
Recycling efforts also include the use of recycled packaging. Many companies now use packaging made from recycled paper. This reduces the overall environmental impact.
Future Innovations
The golf ball industry is evolving fast. New technologies and trends shape its future. Golfers can expect exciting changes in the years ahead.
Technological Advances
Technological advances are driving golf ball innovation. Engineers use nanotechnology to enhance ball performance. Nanoparticles in the core improve compression and distance. These balls can travel farther and provide better control.
Another breakthrough is the use of smart materials. These materials adapt to different temperatures and weather conditions. Golfers can play consistently in any climate. The ball’s durability also increases with these advanced materials.
3D printing is another game-changer. Manufacturers can create complex designs with precision. This technology allows for customization to fit individual playing styles. Golfers can have balls tailored to their needs.
Upcoming Trends
Upcoming trends in golf balls focus on sustainability and environmental impact. Eco-friendly materials are gaining popularity. These materials are biodegradable and reduce waste.
Another trend is the integration of smart technology. Golf balls with embedded sensors can track performance data. Golfers can monitor speed, spin, and trajectory in real-time. This data helps improve skills and strategies.
Personalization is also on the rise. Golfers can now order balls with custom colors, logos, and designs. This trend makes the game more enjoyable and unique.
Lastly, virtual reality (VR) training is becoming a trend. VR-compatible golf balls provide immersive practice experiences. Golfers can simulate real-world courses and improve their game from home.
Credit: www.quora.com
Frequently Asked Questions
How Is A Golf Ball Made Steps?
A golf ball is made through these steps: core molding, rubber winding, cover molding, painting, and finishing.
How To Create A Golf Ball?
To create a golf ball, mold a rubber core. Surround it with rubber threads. Coat with a durable dimpled cover.
What Is The Inside Of A Golf Ball Called?
The inside of a golf ball contains a core made of rubber or synthetic materials, surrounded by layers of different polymers.
How Many Golf Balls Are Made Each Year?
Approximately 1. 2 billion golf balls are produced each year. This massive production meets global demand.
Conclusion
Crafting a golf ball involves precision, innovation, and quality materials. Each layer plays a crucial role in performance. Understanding this process enhances appreciation for the game. Next time you tee off, remember the meticulous craftsmanship behind every shot. Stay tuned for more insights into the fascinating world of golf.